


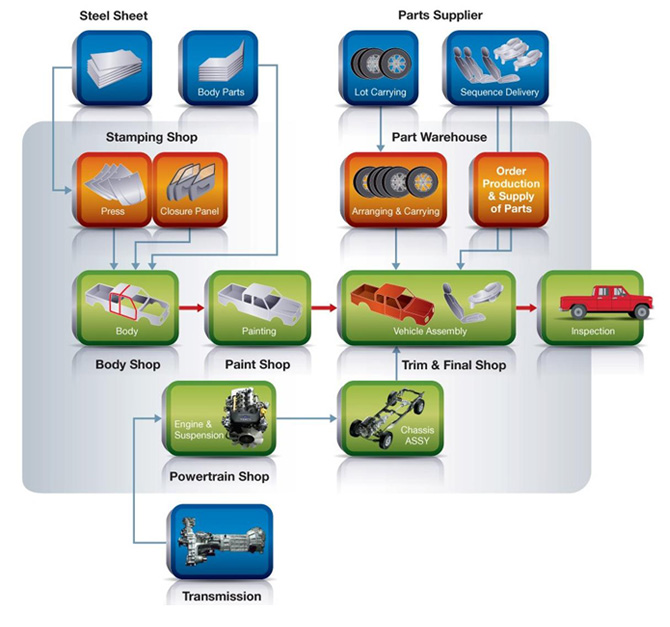

The AAT stamping shop produces metal automotive parts via the use of stamping machines, which press products outer part and inner part. The stamping shop comprises three fully automated production lines (Line A Line B and Line C)
Production line
1. Line A consist of 5 press machine and 7 automatic robot.
2. Line B consist of 5 press machine and 7 automatic robot.
3. Line A consist of 4 press machine and 6 automatic robot.
Allowing for exceptionally high-quality standards. The stamping shop serves as a model Production Line Control (PLC) system in the company.
The car bodies from AAT's own in-house body shop are brought here for paint work. All processes are controlled by the CCS system. The paint's E-coating and sealing process offer excellent rust prevention and water proofing. For Painting process ,Mazda corporation Japan have been developed 3 wet coating system and then apply for Paint shop since 2008.There are 3 main targets as like this |
1) Reduction of VOC (Volatile organic Chemical) production 2) Reduction of CO2 emission 3) Synchronized production |
Key development technology |
1) High quality paint technology Virtual verification technology |
Consist of Four main processes are Short Block line, Cylinder Head line , Long block line and Test loop area
- All main engine component are installed at Short block line.
- Cylinder Head are prepared and installed Intake & Exhaust valve including valve leak test process at Cylinder Head line sent completed cylinder head to install at Short block line.
- Main component which have complexity are prepared by Kitting line then sent to installed at Long block line.
- Completed engine are performed Cold test and Final buy off at Test loop area.
Unit 1 - 3 : Trim part assembly
Unit 4 : Cabin and box matching
Unit 5 and 6 : Final line
Unit 7-10 : Material Handling
In addition to these, there is also a section dedicated to taking care of any incomplete assembly
jobs, known in the industry as Reprocessing.
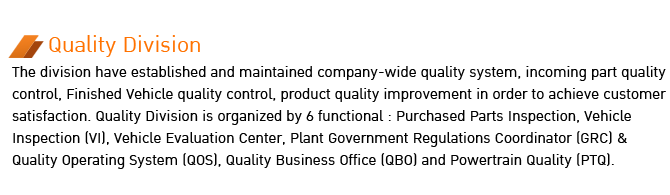
- Establish and maintain purchased parts quality based on standards of design drawing, engineering specifications and governments’ requirements.
- onduct parts audit and protect outflow of parts quality concerns to manufacturing process.
- Administered interim containment actions to protect assembly line and CKD operations when a confirmed defect from purchased parts is identified
The department has both New Vehicle Quality Evaluation and On-going Vehicle audit groups, the process is as below
- Perform off-line audit of vehicles for items that required by quality control plan, external customer, VRT, regulation requirement and parent company policy. The audit teams are FCPA, Air Leak, Water Leak, Wiper Arm Force and Attached Angle, Seal Gap, Fit & Finish, Door Closing Speed, Window Closing Speed, Wheel Alignment, Clear Vision, Head Lamp Aiming, Exhaust Emission, Weight, Dimension, Weight, Parking Brake, Pass-by Noise, CTQ, FER and Squeak and Rattle.
- Evaluate new model vehicle quality.
- Conduct instrument control (an instrument used for precision measurement).
- Interface with the customers to obtain standard quality metric.
- Promote quality improvement activities.
- Establish, promote, maintain and improve the Company’s Quality assurance system under ISO9001 and Parent companies' unique requirements.
- Establish and maintain vehicle quality standards based on engineering specification, customers and Government Regulations’ requirements.
- Provide Quality inspection equipment or machines for Finished Vehicle products testing.
- Provide plant wide customer data
- Facilitate the quality review event
- Promote quality improvement activities
- Establish and maintain purchased parts for Puma engine quality based on standards of design drawing, engineering specifications and governments’ requirements.
- Conduct parts audit for Puma engine by sample and protect outflow of Puma engine parts quality concerns to manufacturing process.
- Administered interim containment actions to protect assembly line and CKD operations when a confirmed defect from purchased parts for Puma engine is identified
- Perform audit COP test (engine performance test) for completed Puma engine
- Perform Dock audit for assembled engine quality by visual check
- Perform audit contamination level for 5C parts (Cylinder Block, Cylinder Head, Crankshaft, Connecting Rod and Camshaft) and Fuel contamination level.
